A quick definition of “Biomimicry” is the adaptation of natural phenomena in solving human problems. In this “green-thinking” society we extract from nature to project advances in the sciences, medicine, transportation, etc. It’s the scientific “in” thing to emulate nature in any form. However, we may also argue that this is nothing new, having been practiced throughout human development and more recently named .
Hydronics for example made great strides with the Romans evidenced by structuring impressive aqueducts for water service and heated public baths in their cities. Things then stagnated until the Industrial Revolution when necessity and invention leapt us into central hydronic heating systems utilizing water in both liquid and vapor stages, i.e. gravity hot water and steam heating respectively. They were and are the simplest and most efficient heating devices. Just maintain a controlled fire in a boiler and let natural hydronic convection deliver energy to the radiation via a closed loop. Too simple, but too limited in flexibility, or were they? (Fig. 1)
The gravity heating system ended with the introduction of the hydronic circulator about 1930. Now we have individually controlled multiple heating zones utilizing smaller boilers, flexibly piped to varied perimeter, wall and floor radiation with finite control. Life is good, at least on the surface. We have developed highly refined hydronic components, assimilated to create the new hydronic heating algorithm, but at a hidden energy cost and performance potential. Let’s elaborate.
The major drawbacks to gravity heating were the need for a large boiler, piping and radiators, providing single zone heating. Fuel efficiency wasn’t so hot but fuel prices were rock bottom. The transitional improvements within hydronic heating components to the present are commendable, to a point. Lots of components, design flexibility and controls provide a great applications menu with arguably “new” algorithms, but what about that natural, unpowered heating algorithm?
In 1975 we began experimenting with gravity-assisted heating after convective-coupling (with no circulator) our old-style flow-checked, circulators-on-returns FHW System to a salvaged 1935 International Heater No. 64 Wood Burner museum piece. Our then new raised ranch home had three naturally balanced split loop zones with modestly pitched 1” supplies and returns. Here in rural “Frostbite Falls” New England we are vulnerable to severe Nor’Easter Snow with occasional Ice Storms to boot. By experimentation we discovered that we could empirically open/adjust flow check valves to meet full heating demands. Fire up the Ol’ International with wood and twiddle the valves ….. No electricity required! Recall doing it for a week once, baby-sitting my “Beast”.
As a career Manufacturing Process Engineer I would like to offer a tenet of process engineering. When justifying a process change you provide two justifications: One, optimization cost and benefits of the current process, and Two, the same with the new process. A decision is then made by qualifying and quantifying the benefits of each within your business plan. Do otherwise at your peril, as I have ….. But you’ll do it only once!
So let us look at optimizing that naturally simple, tough and reliable natural convection (gravity) heating system by employing modern components and methods.
First, a hydronic heating system comprises three (3) basic elements:
- A Boiler (Heated Water Generator), traditionally of cast-iron construction, but now including cast aluminum and fabricated stainless steel water tube constructions.
- Heated Water Distribution, presumably consisting of circulator(s) and various valves with associated piping, wiring and controls.
- Radiation (Heat Dissemination), to acclimate living/occupied spaces along with temperature controls.
Meanwhile the traditional gravity high-mass cast-iron boiler has evolved into a typically lower-massed unit, thus limiting its natural convection potential. The Weil-McLain® UO Series is the highest mass to heating capacity by far of current residential offerings, as compared to contemporaries, both domestic & foreign. Sheer boiler mass typically protracts operating life under field conditions; in particular to thermal shocking and magnetite accommodation (iron is a natural scavenger). Curiously the cost per pound of the Weil UO (divide boiler weight into cost) is up to 1/2 that of all others. Interesting ….. Now just what are we paying for?
We selected the Beckett NX Pressure-Fired Oil Burner for our development. (Gas equivalents are also available.) Thus we may atmospherically or optionally direct vent without issue and in most applications.
A decade ago delta-t circulators appeared, specifically the Taco® VDT, the “BumbleBee”, the Viridian and 00e Series in succession. We researched and discarded the VDT as potentially problematic but then jumped in with the BumbleBee offering. Then Taco heard of our work and offered Viridian upgrades. “The rest is history” as they say. The Taco® VT2218 ΔT ECM Circulator matches the Weil-McLain® UO Series profile so well. BTW – we call this “putting an ‘automatic transmission’ on a boiler”. Further combining with Taco® Zone Sentry Valves defines the lowest distribution energy delivery system available. However, some mechanical energy is still desirable to facilitate control while satisfying variable heating demands. Thus we can accommodate typically smaller diameter distribution piping than the old “gravities” required with reasonable energy consumption. We also like to think of this as “like paddling your canoe with the current”, if you please.
Gravity system emulation is achieved by minimizing and compacting “near-boiler” all-iron distribution piping with zone valving directly above a high-mass boiler. All distribution piping is contained within the boiler “footprint”, contrary to contemporary practice, substantially reducing material, labor and system costs. By further defining distinct and variable Boiler, Supply and Return Modules provides a simple menu accommodating most residential applications. Our patented designed-for-manufacture “appliance” approach enables “Economies Of Scale” production from material procurement through processing to the “Point Of Sale”. It remains only to “extend the pipes and wires” for installation completion. (Fig. 2)
Domestic Hot Water (DWH) Generation via integration with an HTP® SuperStor Max Indirect Water Heater (IWH) is a natural extension of hydronic heating. This attribute was not practical within the gravity heating system of old but is within a modernized, convection-assisted appliance. The immediate benefit is virtually “free” DHW during the heating season with minimal and potentially programmable cycling in the off-season.
Importantly, hydronically prioritizing via close-coupling the DHW Option within our near-boiler piping architecture demonstrates continued, extended heating capabilities:
- A VT2218 system circulator shutdown continues reduced, auto-convection induced heating indefinitely. Fault recognition time will vary with site radiation conditions however.
- Similarly to date, no DHW generation interruption has been noted under the VT2218 Fail Condition. A close-coupled and thus de facto priority convection loop works!
- A burner (boiler energy supply) failure initiates a system energy draw-down to potentially ambient temperature. If IWH Optioned, the DHW tank thermal capacity is included in the draw down via zone valve actuated heating coil operation.
Try these with a “conventional” hydronic heating system!
As an aside, isn’t there a current discussion of coupling a “buffer tank” to Combi-Boilers to alleviate their short-cycling tendencies? Just mentioning …..
As prior inferred, radiation zone type and configuration is the determinant of natural convection effect upon area heating. Thus, radiant zone(s) in particular will necessarily be branched and configured as currently off the supply header and returned upper and/or lower as opportune.
We currently monitor ten (10) “Beta” installations in a variety of applications, and having now aggregated over fifty (55) installed-years and 200,000 hours of operation. These range from 2800 sq. ft. new homes to a “Tack Shop”, all using the same Beckett® NX oil-fired Weil-McLain® UO-3 boiler with varying Supply & Return Modules, including a direct vented unit. Two (2) units are new hydronic installs, the remainder being boiler replacements.
All of our appliances exhibit a VT2218 circulator distribution energy consumption of 8 to 13 watts beyond delta-t differential achievement! This is half or less that anticipated by Taco® for this application and well over 90% minimum energy reduction over any contemporary system.
System operating temperatures upon delta-t achievement typically vary from 132°F to 155°F, substantially lowered from their lower-massed replacements. However, a recent new install coupled to a prior hydronic wood boiler system exhibited a 165°F average system temperature. A dominant zone demand was determined to have a 35% zone radiation deficiency to be corrected.
Boiler burner cycling is not only substantially reduced, but we have experimented with maintenance intervals up to five (5) years without consequence. Our recent three annual servicings had absolutely NO heat exchanger debris (soot or ash)! To date we have had no system-related service calls ….. None! It’s not only the “Maytag® Repairman” that is lonesome these days.
So, we have effectively re-engineered the current residential hydronic heating process toward optimization using biomimicry, et al. A simple, durable, flexible and efficient product has evolved that installs and operates for less and with twice or more (?) the operating life. Referring to the 2019 Annual Boiler Report, a participant opined that “many customers are still looking for the long-term dependability of cast iron. When you really factor in everything from the cost of the boiler, installation cost, maintenance costs and life expectancies, cast iron is still a very sound choice”. Yes, and it just got better. (Fig. 3)
The residential hydronic heating industry, despite being the most efficient means of creating warmth has been steadily losing market share, and recently more rapidly! The blame rests solely upon the industry participants and the reason is simple. There has been no incentive within the totally component-driven hydronic heating market to change anything but to continue its part-selling competition. Meanwhile the consumer is paying for the unproductive enterprise of free-lance hydronic heating installations, but they and the competition are smartening up.
Over a century ago there were the “Carriage Makers” who hand-built carriages. Then the “Horseless Carriage” (a.k.a. Automobile) arrived and they continued hand-built automobiles. Everyone built a few and sold a few that everyone could use, but not afford. One of them, Henry Ford value-engineered and methodized his “Model T” that everyone could afford. The rest is history ….. Now, perhaps it’s time for the Hydronic “Model ΔT”?
Paul D. Mercier, Sr. 06/30/2021 (Updated 02/20/2023)
Mercier Engineering
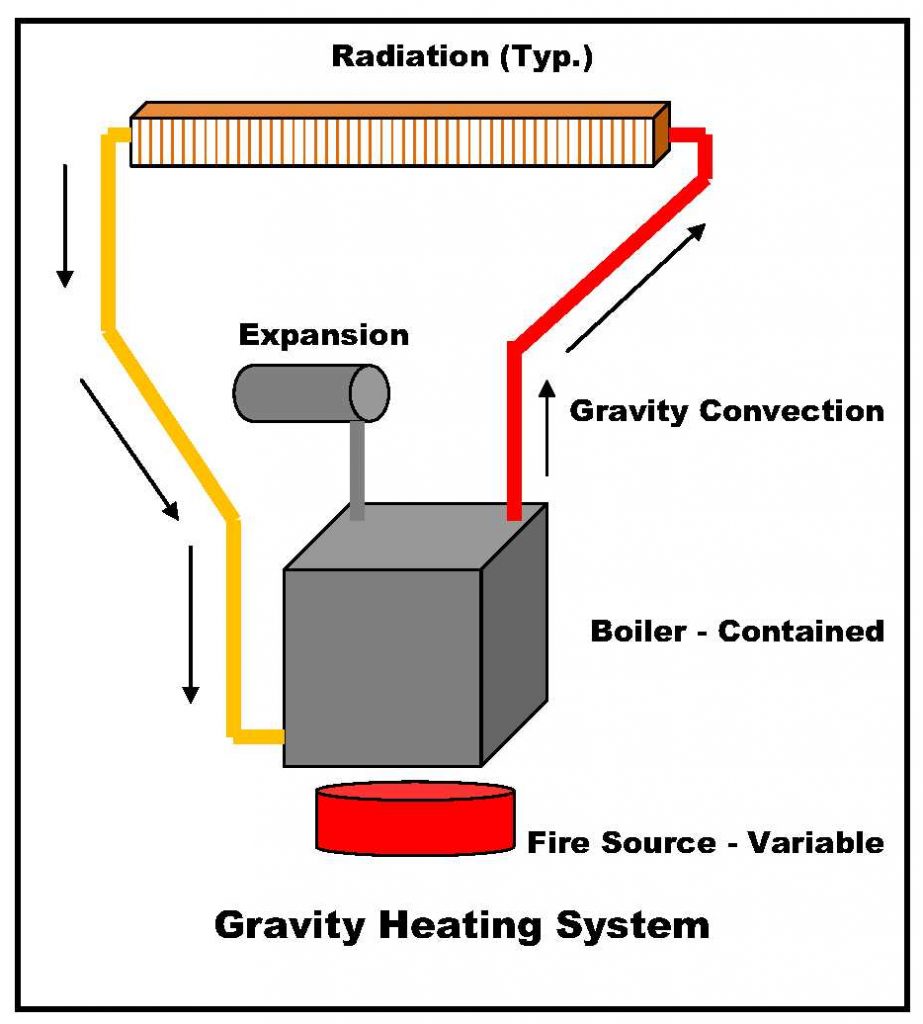
Fig. 1
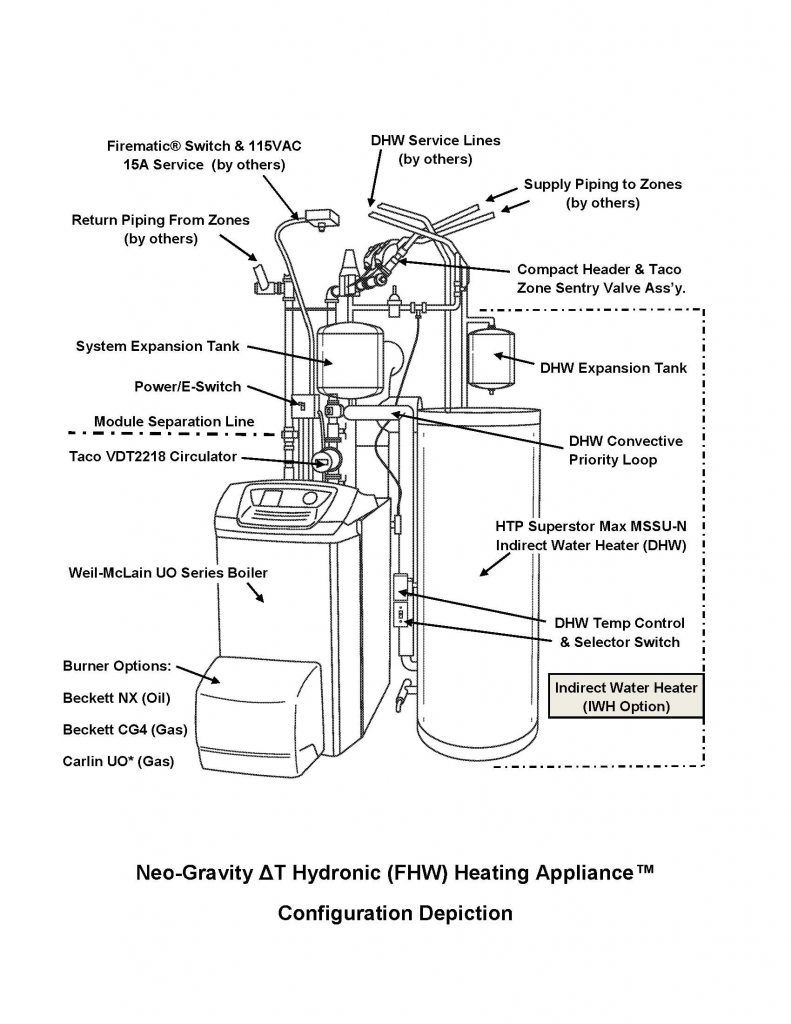
Fig. 2
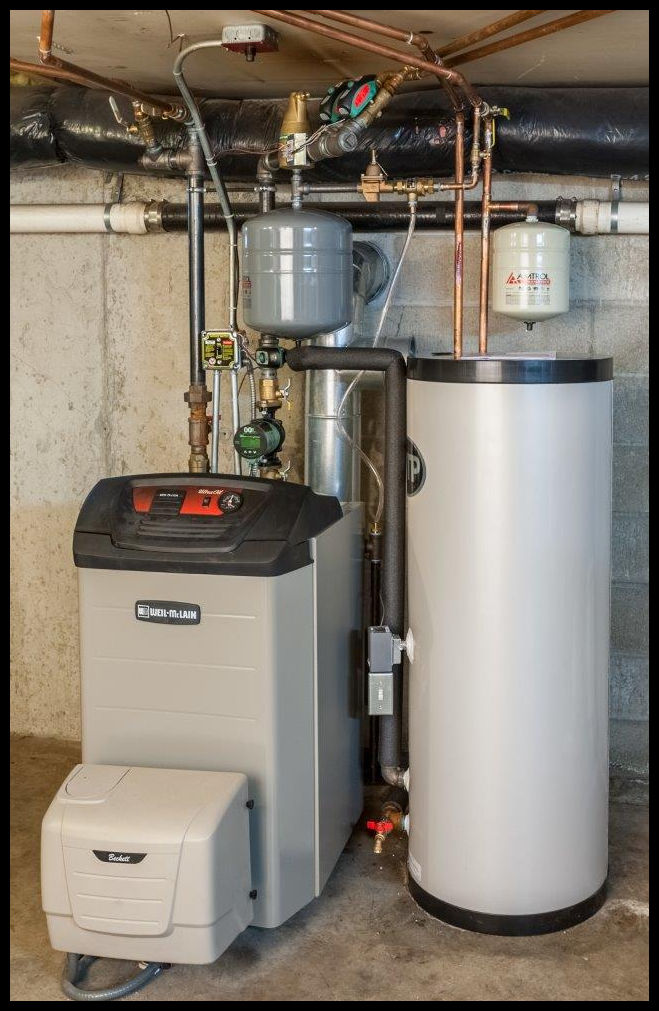
Fig. 3
Paul D. Mercier, Sr. is a career Manufacturing Process Development Engineer, studying Mechanical Engineering at L’Université d’Ottawa, Canada. A parallel Hydronic Heating Engineering enterprise from a family trades business has both preceded and ensued. Recently awarded U.S. Patent 10,690,356 and Canada 2,964,131 on an “ENHANCED CONVECTION, DIFFERENTIAL TEMPERATURE MANAGED, HYDRONIC HEATING APPLIANCE” and d-b-a Boilers On Demand, Antrim, NH USA. He can be reached at BoilersOnDemand.com, Facebook, 603-588-2333 or .